Bộ Điều Khiển Lập Trình PLC Hiện Nay
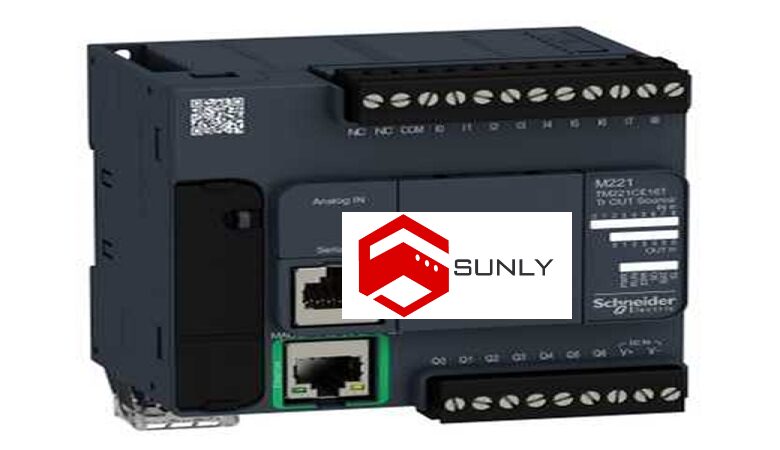
Bộ Điều Khiển Lập Trình PLC, viết tắt của Programmable Logic Controller, là một thiết bị kỹ thuật số được thiết kế để điều khiển các quy trình tự động trong công nghiệp. PLC là một phần quan trọng trong các hệ thống tự động hóa, giúp cải thiện hiệu suất và độ chính xác của các quy trình sản xuất và vận hành công nghiệp.
Bộ Điều Khiển Lập Trình PLC là gì?: Những Điều Bạn Cần Biết
Lịch sử của PLC bắt đầu từ cuối thập niên 1960 khi các nhà sản xuất ô tô cần một giải pháp linh hoạt hơn để thay thế các hệ thống điều khiển relay truyền thống. Đại lý Proface tại Việt Nam Richard Morley, được coi là “cha đẻ” của PLC, đã phát triển bộ điều khiển đầu tiên cho General Motors vào năm 1968. Kể từ đó, PLC đã trải qua nhiều giai đoạn phát triển và cải tiến, trở thành một công cụ không thể thiếu trong các ngành công nghiệp hiện đại.
Ngày nay, PLC được sử dụng rộng rãi trong nhiều lĩnh vực khác nhau như sản xuất, dầu khí, năng lượng, thực phẩm và đồ uống, nước và xử lý nước thải, cũng như trong các ứng dụng xây dựng và cơ sở hạ tầng. Sự phổ biến của PLC được thúc đẩy bởi khả năng lập trình linh hoạt, độ tin cậy cao, và khả năng tích hợp dễ dàng với các hệ thống điều khiển và giám sát khác.
PLC hoạt động bằng cách thực hiện các lệnh lập trình sẵn để điều khiển các thiết bị và quy trình công nghiệp. Các lệnh này được viết bằng các ngôn ngữ lập trình đặc thù như Ladder Logic, Structured Text, hoặc Function Block Diagram. Nhờ vào khả năng lập trình này, PLC có thể dễ dàng tùy chỉnh và điều chỉnh để đáp ứng các yêu cầu cụ thể của từng ứng dụng.
Với sự tiến bộ không ngừng của công nghệ, PLC ngày càng trở nên mạnh mẽ hơn, hỗ trợ các giao thức truyền thông hiện đại và tích hợp với các hệ thống Internet of Things (IoT). Điều này mở ra nhiều cơ hội mới cho việc tối ưu hóa quy trình và tăng cường hiệu quả sản xuất trong kỷ nguyên số hóa.
Cấu Trúc và Thành Phần Cơ Bản của PLC
Một bộ điều khiển lập trình PLC (Programmable Logic Controller) bao gồm nhiều thành phần chính, mỗi thành phần đảm nhận vai trò cụ thể trong việc thực hiện các nhiệm vụ điều khiển. Đại lý Watanabe tại Việt Nam Cấu trúc vật lý của PLC thường bao gồm CPU, bộ nhớ, các module I/O, và hệ thống nguồn. Hiểu rõ chức năng và cách các thành phần này tương tác là nền tảng để khai thác tối đa khả năng của PLC.
CPU (Central Processing Unit) là trái tim của PLC, chịu trách nhiệm thực hiện các chương trình điều khiển và xử lý dữ liệu. CPU nhận tín hiệu từ các đầu vào, xử lý theo logic được lập trình và gửi tín hiệu đến các đầu ra để điều khiển các thiết bị khác nhau. Tốc độ và hiệu suất của CPU quyết định khả năng xử lý và thời gian phản hồi của hệ thống.
Bộ nhớ của PLC chia làm hai loại chính: bộ nhớ chương trình và bộ nhớ dữ liệu. Bộ nhớ chương trình lưu trữ các chương trình điều khiển được viết bằng ngôn ngữ lập trình PLC, trong khi bộ nhớ dữ liệu lưu trữ các biến và trạng thái của hệ thống trong quá trình vận hành. Các loại bộ nhớ phổ biến bao gồm RAM, ROM, và EEPROM, mỗi loại có ưu và nhược điểm riêng.
Các module I/O (Input/Output) là cầu nối giữa PLC và các thiết bị ngoại vi như cảm biến, công tắc, động cơ, và van. Module đầu vào nhận tín hiệu từ các cảm biến và bộ chuyển đổi, trong khi module đầu ra gửi tín hiệu điều khiển đến các thiết bị thực thi. Các module I/O có thể được mở rộng để phù hợp với yêu cầu cụ thể của từng ứng dụng.
Hệ thống nguồn cung cấp điện cho toàn bộ PLC và các module liên quan. Nguồn điện ổn định và đáng tin cậy là yếu tố quan trọng để đảm bảo hoạt động liên tục và chính xác của hệ thống điều khiển tự động.
Tổng hợp lại, cấu trúc và thành phần cơ bản của PLC không chỉ cung cấp khả năng điều khiển mạnh mẽ mà còn đảm bảo tính linh hoạt và khả năng mở rộng cho các ứng dụng công nghiệp đa dạng.
Nguyên Lý Hoạt Động của PLC
Bộ điều khiển lập trình PLC (Programmable Logic Controller) là một thiết bị quan trọng trong tự động hóa công nghiệp. Hiểu rõ nguyên lý hoạt động của PLC là yếu tố then chốt để tối ưu hóa hiệu suất của hệ thống. PLC hoạt động dựa trên một chu trình quét, gọi là scan cycle, bao gồm ba giai đoạn chính: đọc đầu vào, xử lý logic, và xuất đầu ra.
Giai đoạn đầu tiên trong chu trình quét là đọc đầu vào. PLC nhận các tín hiệu từ các thiết bị đầu vào như công tắc, cảm biến nhiệt độ, và cảm biến áp suất. Các tín hiệu này có thể ở dạng số (digital) hoặc dạng tương tự (analog). PLC sẽ chuyển đổi các tín hiệu tương tự thành tín hiệu số để xử lý dễ dàng hơn.
Sau khi nhận tín hiệu đầu vào, PLC tiến hành giai đoạn xử lý logic. Trong giai đoạn này, PLC sử dụng các chương trình đã được lập trình sẵn để phân tích các tín hiệu đầu vào và thực hiện các phép toán logic như AND, OR, NOT, và XOR. Các chương trình này thường được viết bằng ngôn ngữ lập trình đặc biệt dành cho PLC, chẳng hạn như Ladder Logic hoặc Function Block Diagram.
Cuối cùng, PLC thực hiện giai đoạn xuất đầu ra. Sau khi hoàn thành các tính toán logic, PLC sẽ gửi tín hiệu điều khiển đến các thiết bị đầu ra như động cơ, van, hoặc màn hình hiển thị. Các tín hiệu đầu ra có thể là tín hiệu số để bật/tắt thiết bị, hoặc tín hiệu tương tự để điều chỉnh mức độ hoạt động của thiết bị.
Toàn bộ quá trình từ đọc đầu vào, xử lý logic, đến xuất đầu ra diễn ra rất nhanh chóng, thường chỉ trong vài mili giây. Chu trình quét này lặp lại liên tục, đảm bảo rằng hệ thống luôn cập nhật và phản ứng kịp thời với các thay đổi từ môi trường xung quanh. Hiểu rõ các bước trong chu trình quét của PLC giúp người vận hành và kỹ sư có thể tối ưu hóa và khắc phục sự cố nhanh chóng, nâng cao hiệu quả và độ tin cậy của hệ thống tự động hóa.
Lợi Ích của Sử Dụng PLC trong Công Nghiệp
Trong bối cảnh công nghiệp hiện đại, việc sử dụng bộ điều khiển lập trình PLC mang lại nhiều lợi ích đáng kể, góp phần nâng cao hiệu suất và độ tin cậy của các quy trình sản xuất. Một trong những lợi ích quan trọng nhất của PLC là khả năng tăng hiệu suất. PLC có thể thực hiện các thao tác điều khiển với tốc độ cao và độ chính xác lớn, giúp giảm thời gian chết và tối ưu hóa quá trình sản xuất. Điều này có thể dẫn đến tăng năng suất và giảm chi phí sản xuất.
Độ tin cậy cao là một lợi ích khác khi sử dụng PLC trong công nghiệp. PLC được thiết kế để hoạt động liên tục trong môi trường công nghiệp khắc nghiệt, chịu được nhiệt độ cao, độ ẩm và rung động. Những yếu tố này giúp PLC trở thành một giải pháp điều khiển ổn định và đáng tin cậy, giảm thiểu nguy cơ hỏng hóc và ngừng hoạt động không mong muốn.
Khả năng kiểm soát linh hoạt của PLC cũng là một ưu điểm quan trọng. PLC có thể được lập trình để thực hiện nhiều chức năng khác nhau, từ các tác vụ đơn giản như điều khiển đèn chiếu sáng đến các quy trình phức tạp như điều khiển dây chuyền sản xuất tự động. Điều này tạo điều kiện cho các nhà máy và xí nghiệp dễ dàng điều chỉnh quy trình sản xuất theo nhu cầu thực tế, cải thiện tính linh hoạt và khả năng đáp ứng nhanh chóng.
Cuối cùng, PLC còn mang lại lợi ích về mặt dễ dàng bảo trì. Với giao diện người dùng thân thiện và khả năng tự chẩn đoán lỗi, việc bảo trì và sửa chữa PLC trở nên đơn giản và nhanh chóng hơn. Điều này không chỉ giúp tiết kiệm thời gian mà còn giảm chi phí bảo trì, nâng cao hiệu quả sử dụng thiết bị trong dài hạn.
Ứng Dụng Thực Tiễn của PLC
Bộ điều khiển lập trình PLC (Programmable Logic Controller) đóng một vai trò quan trọng trong nhiều ngành công nghiệp hiện đại. Chúng không chỉ giúp tối ưu hóa quy trình sản xuất mà còn tăng cường hiệu quả và độ tin cậy của hệ thống. Dưới đây là một số ví dụ cụ thể về ứng dụng thực tiễn của PLC trong các lĩnh vực khác nhau.
Trong ngành sản xuất, PLC được sử dụng để điều khiển các dây chuyền sản xuất tự động. Chẳng hạn, trong ngành công nghiệp ô tô, PLC điều khiển robot hàn, lắp ráp và sơn. Điều này không chỉ giảm thiểu sai sót mà còn tăng năng suất và đảm bảo chất lượng sản phẩm. Một ví dụ khác là trong ngành đóng gói, PLC điều khiển các máy đóng gói, cân và dán nhãn, giúp đảm bảo sự đồng nhất và tối ưu hóa quá trình sản xuất.
Trong lĩnh vực tự động hóa tòa nhà, PLC được sử dụng để quản lý hệ thống sưởi, thông gió và điều hòa không khí (HVAC). Các hệ thống này có thể được lập trình để điều chỉnh nhiệt độ và luồng không khí dựa trên các điều kiện môi trường và nhu cầu sử dụng. Ngoài ra, PLC còn được sử dụng để điều khiển ánh sáng, an ninh và các hệ thống quản lý năng lượng khác, giúp tối ưu hóa việc sử dụng tài nguyên và giảm chi phí vận hành.
Xử lý nước thải cũng là một lĩnh vực mà PLC thể hiện rõ khả năng của mình. Các hệ thống xử lý nước thải sử dụng PLC để điều khiển quá trình bơm, lọc và xử lý hóa học. Điều này giúp đảm bảo rằng nước thải được xử lý đúng cách và tuân thủ các quy định về môi trường. Việc sử dụng PLC trong lĩnh vực này không chỉ tăng cường hiệu quả xử lý mà còn giảm thiểu rủi ro ô nhiễm.
Ngoài ra, PLC còn được ứng dụng trong nhiều lĩnh vực khác như tự động hóa sản xuất thực phẩm và đồ uống, điều khiển hệ thống năng lượng tái tạo, và quản lý hệ thống điện lưới. Khả năng lập trình linh hoạt và độ tin cậy cao của PLC làm cho chúng trở thành một công cụ không thể thiếu trong việc tối ưu hóa và tự động hóa các quy trình công nghiệp.
Bài viết xem thêm : Đại Lý Phoenix Contact Tại Việt Nam